/bd7ef515-0570-479b-9b51-889e5bf00067.png)
Voc Six Sigma Example
Review Rating Score
Six Sigma is a highly effective methodology that aims to improve the quality of business processes by eliminating defects and reducing variations. One crucial component of this methodology is Voice of the Customer (VOC), which involves capturing and understanding customer needs and expectations. In this article, we will explore a real-life example of how VOC was used in a Six Sigma project and its impact on improving process quality.
Understanding Voice of the Customer (VOC)
Voice of the Customer refers to the process of gathering and analyzing customer feedback, preferences, and expectations. By collecting VOC data, organizations gain valuable insights into what customers truly value, allowing them to align their processes and offerings accordingly. VOC plays a critical role in Six Sigma projects as it directs the focus towards customer satisfaction and drives continuous improvement.
A Real-life VOC Six Sigma Example
Let's consider a hypothetical scenario in which a manufacturing company wants to improve the quality of their products. By implementing Six Sigma, the company decides to utilize VOC to gain a better understanding of customer requirements and identify areas for improvement.
The VOC process begins with collecting data from customers through surveys, interviews, or other feedback channels. The company discovers that customers are experiencing issues related to product durability and reliability. These insights are then analyzed, and the critical elements are identified.
Based on the VOC data analysis, the company identifies specific improvement opportunities, such as enhancing the product manufacturing process, using higher quality materials, and improving quality control measures. They implement these changes and measure the results to ensure effectiveness.
The Impact of VOC on Process Quality
By leveraging VOC data and implementing the necessary improvements, the manufacturing company can experience significant improvements in process quality. Here are some key benefits:
- Customer Satisfaction: By addressing customer needs and expectations, the company can enhance customer satisfaction, loyalty, and retention.
- Reduced Defects: Implementing changes based on VOC insights helps identify defects early in the process, leading to a reduction in defects and rework.
- Streamlined Processes: VOC analysis provides valuable insights into streamlining processes, reducing cycle time, and eliminating non-value-added activities.
- Improved Reputation: By consistently meeting customer expectations, the company can build a positive reputation in the marketplace.
Download Our VOC Six Sigma Example PDF
If you want to see a practical example of how VOC was implemented in a Six Sigma project, download our VOC Six Sigma Example PDF. This comprehensive case study provides detailed insights into the VOC process, data collection methods, analysis techniques, and the resulting process improvements. Simply visit our website at BizzLibrary.com and start your download now!
Is the template content above helpful?
Thanks for letting us know!
Reviews
Harley Cherry(7/24/2023) - USA
Thank you for the letter!!
Last modified
Our Latest Blog
- The Importance of Vehicle Inspections in Rent-to-Own Car Agreements
- Setting Up Your E-mail Marketing for Your Business: The Blueprint to Skyrocketing Engagement and Sales
- The Power of Document Templates: Enhancing Efficiency and Streamlining Workflows
- Writing a Great Resume: Tips from a Professional Resume Writer
Template Tags
Need help?
We are standing by to assist you. Please keep in mind we are not licensed attorneys and cannot address any legal related questions.
-
Chat
Online - Email
Send a message
You May Also Like
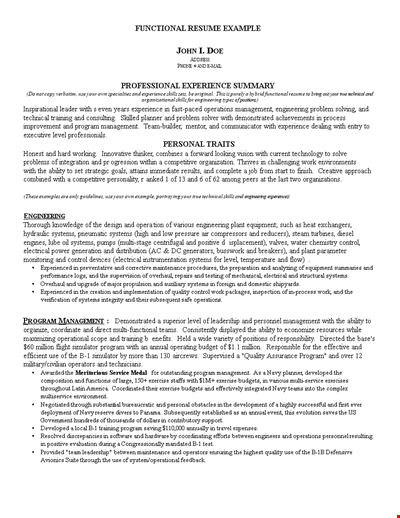
Engineering Functional Program - Quality Management & Training
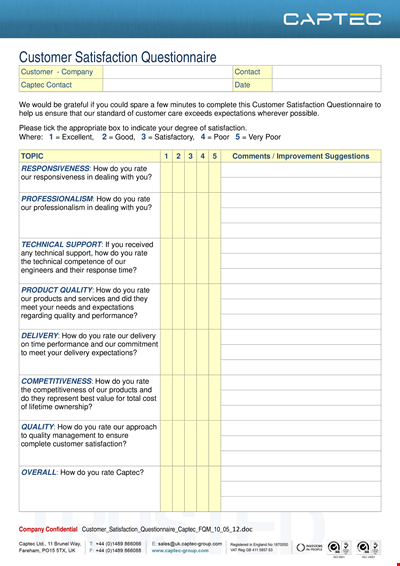
Customer Satisfaction Survey Questionnaire - Ensuring Quality at Captec
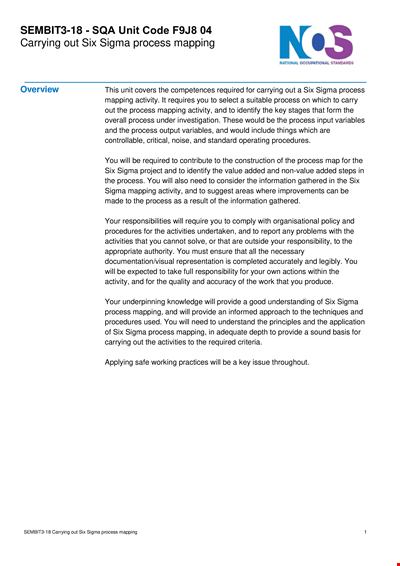
Process Map Six Sigma Example
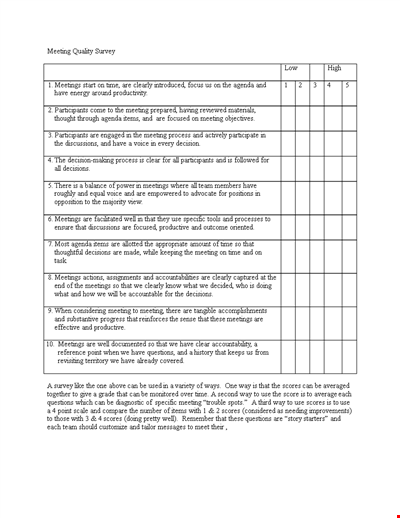
Meeting Quality Survey
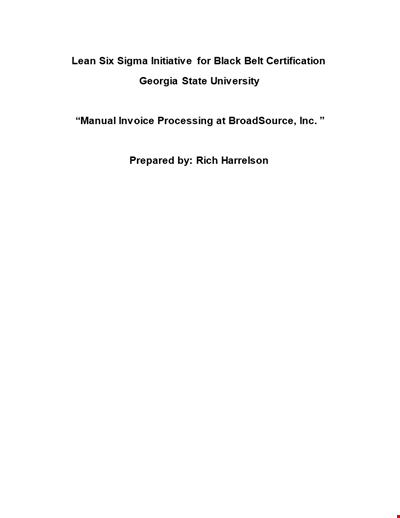
Goal Statement Six Sigma Example
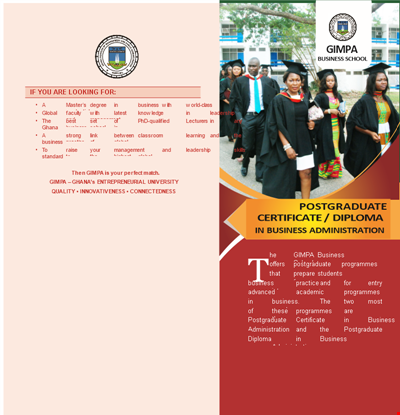
Post Graduate Certificate In Quality Management
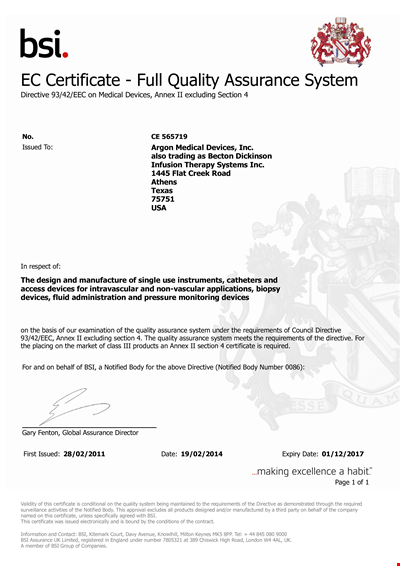
Quality Assurance Management Certificate
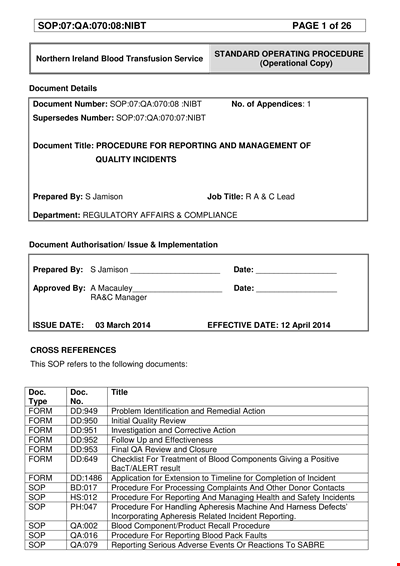
Quality Incident Report Format
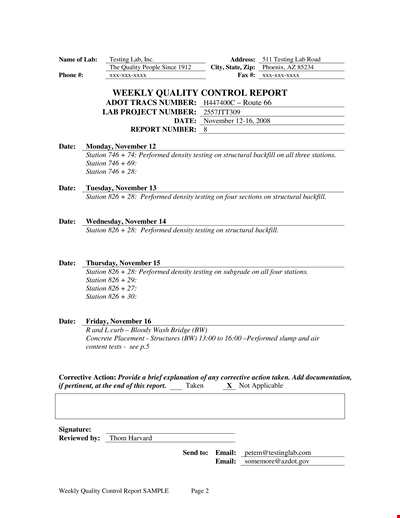
Weekly Quality
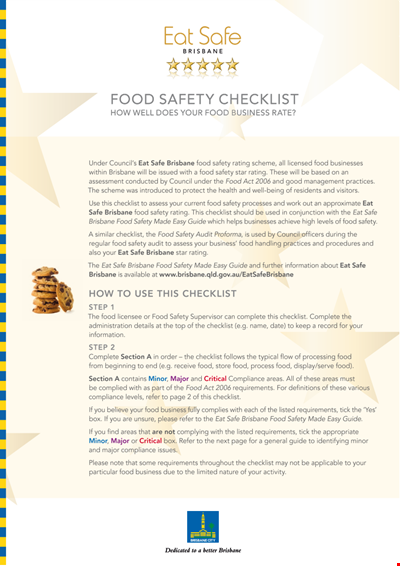
Food Safety Quality Control Checklist Template
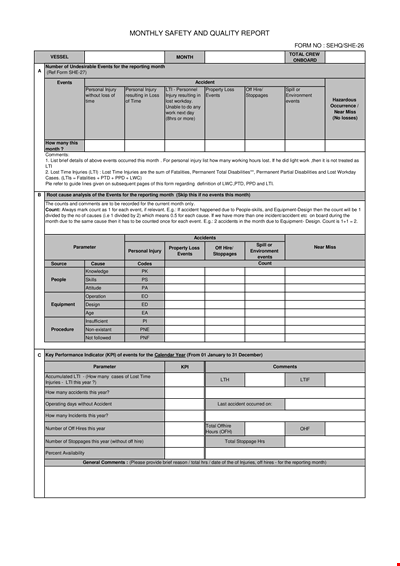
Monthly Quality
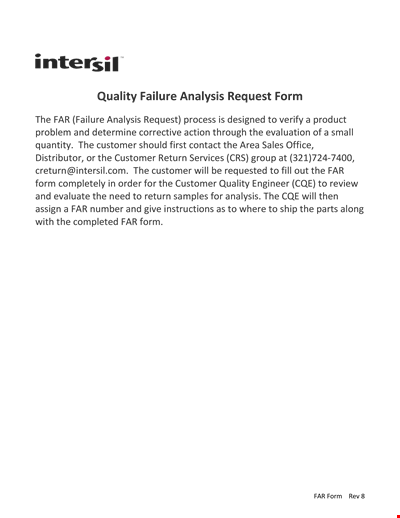
Quality Failure Analysis Request Form
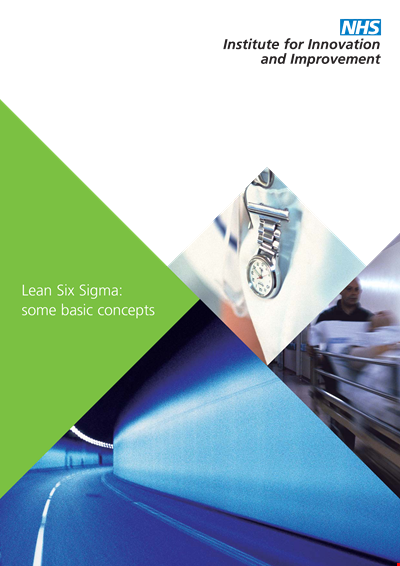
Lean Six Sigma Example - Process Improvement and Value Optimization
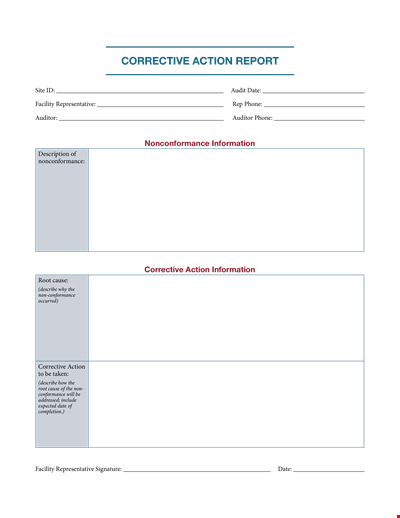
Corrective Action Sample - Improve Facility with Action for Nonconformance
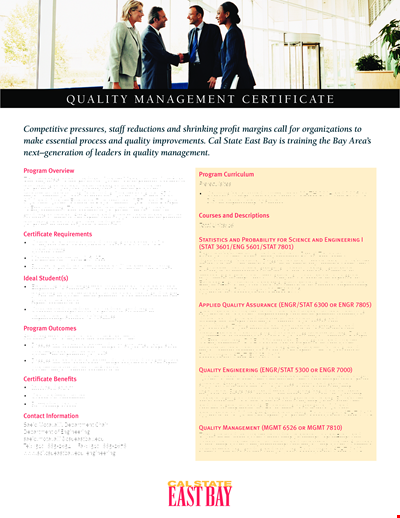
Quality Control Management Certificate Program for Engineering
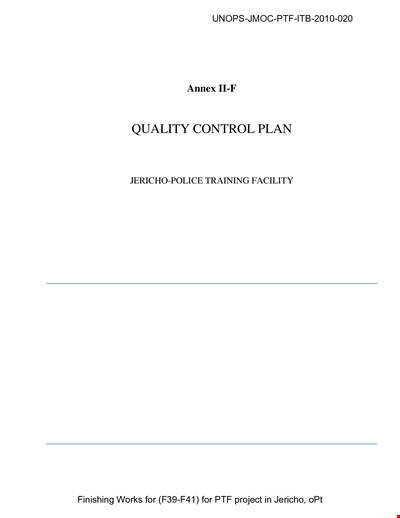
Quality Control Management Plan for Contractors - Unops-Quality Control Management Plan